The Ultimate Guide to Product Packaging Device Repair Work: Maintain Your Operations Running Efficiently
Understanding the details of product packaging equipment repair service is crucial for keeping ideal efficiency and decreasing disturbances. Normal maintenance not only expands the life of these makers however likewise addresses usual problems that can hinder productivity.
Value of Regular Upkeep
Routine maintenance of packaging equipments is important for making certain optimal performance and longevity. By executing an organized maintenance routine, operators can recognize possible concerns before they escalate right into considerable troubles. This proactive strategy not just reduces downtime yet additionally expands the lifespan of the devices, inevitably bring about reduced functional costs.
Regular examinations enable the analysis of crucial elements such as seals, belts, and sensors. Resolving deterioration quickly avoids unforeseen failings that might interfere with manufacturing and bring about pricey repair services. Additionally, routine upkeep helps make sure compliance with sector standards and regulations, cultivating a risk-free functioning atmosphere.
Additionally, maintenance tasks such as calibration, lubrication, and cleaning considerably boost machine efficiency. Boosted efficiency converts to constant item high quality, which is essential for keeping client satisfaction and brand online reputation. A properly maintained product packaging equipment operates at optimum rates and minimizes material waste, adding to total productivity.
Typical Packaging Maker Concerns
Packaging machines, like any type of complex equipment, can encounter a variety of typical problems that may hinder their efficiency and effectiveness - packaging machine repair. One common problem is irregular sealing, which can cause product perishing and wastefulness if bundles are not appropriately secured. This often arises from misaligned parts or worn sealing components
An additional constant issue is mechanical jams, which can happen due to international things, worn parts, or incorrect alignment. Jams can create delays in manufacturing and rise downtime, inevitably impacting general productivity. Furthermore, digital malfunctions, such as failure in sensors or control systems, can lead and disrupt procedures to inaccurate measurements or erratic maker behavior.
In addition, problems with item feed can likewise occur, where items may not be supplied to the product packaging location continually, causing interruptions. Wear and tear on rollers and belts can lead to suboptimal performance, needing immediate attention to protect against further damage.
Comprehending these usual concerns is essential for preserving the stability of packaging operations, making sure that machinery runs efficiently and effectively, which consequently helps in meeting manufacturing targets and preserving product high quality.
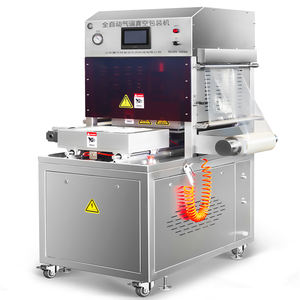
Fixing Techniques
Efficient fixing methods are important for without delay dealing with problems that develop with product packaging machines. A systematic technique is important for recognizing the root cause of malfunctions and reducing downtime. Begin by gathering information regarding the symptoms observed; this might include unusual sounds, functional delays, or error codes presented on the machine's interface.
Next, refer to the device's manual for fixing standards certain to the version in concern. This resource can give useful insights right into usual problems and suggested analysis actions. Use aesthetic assessments to check for loose connections, worn belts, or misaligned components, as these physical factors frequently add to operational failings.
Apply a process of elimination click here now by screening individual maker functions. If a seal is not creating appropriately, evaluate the securing device and temperature level setups to establish if they satisfy functional specs. Document each step taken and the outcomes observed, as this can aid in future repairing efforts.
Repair vs. Substitute Decisions
When encountered with devices malfunctions, choosing whether to fix or replace a packaging device can be a facility and crucial selection. This decision depends upon numerous key aspects, including the age of the device, the degree of the damage, and the forecasted influence on operational effectiveness.
To start with, think about the device's age. Older machines might need even more frequent repairs, bring about higher cumulative prices that can surpass the investment in a brand-new system. Additionally, evaluate the intensity of the breakdown. Small problems can typically be solved swiftly and affordably, whereas extensive damages may demand a substantial economic dedication for repair services.
Functional downtime is an additional vital consideration. Investing about his in a brand-new machine that supplies enhanced performance and dependability might be more prudent if repairing the machine will certainly trigger extended hold-ups. Think about the schedule of components; if substitute parts are hard to come by, it might be more tactical to replace the maker entirely.
Eventually, doing a cost-benefit analysis that includes both long-term and instant effects will certainly help in making an educated choice that aligns with your operational goals and monetary constraints. (packaging machine repair)
Safety Nets for Long Life
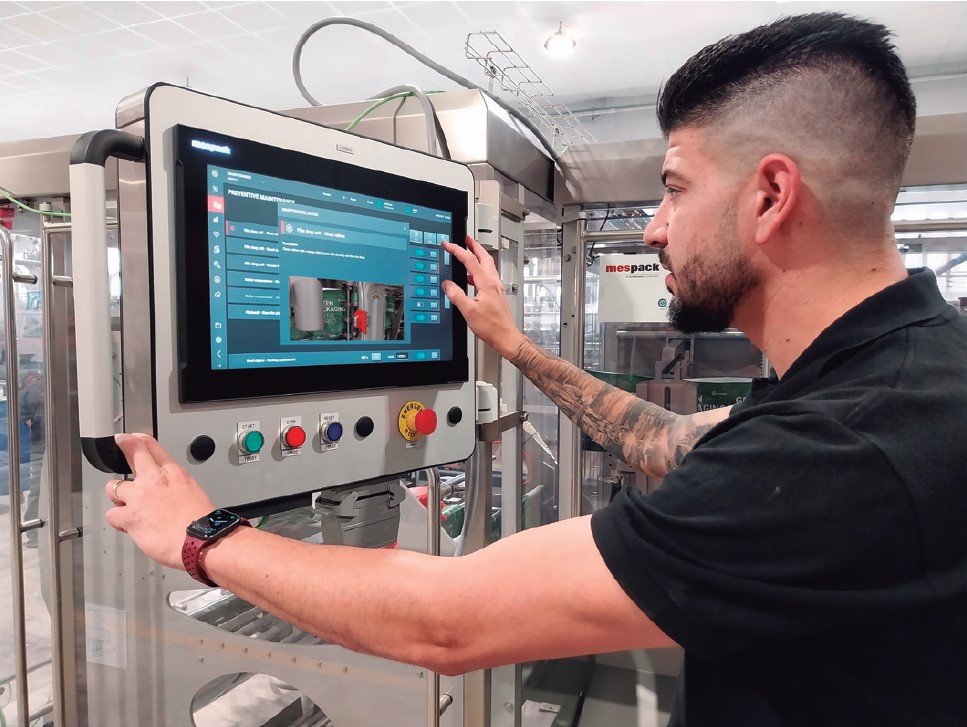
Key safety nets include regular lubrication of relocating components, placement checks, and calibration of controls resource and sensors. Developing a cleansing schedule to eliminate particles and pollutants from equipment can considerably reduce deterioration (packaging machine repair). Additionally, keeping an eye on operational specifications such as temperature and vibration can aid identify abnormalities at an early stage
Educating personnel to acknowledge indications of wear or breakdown is an additional essential component of precautionary maintenance. Equipping operators with the knowledge to execute fundamental troubleshooting can cause quicker resolutions and lessen functional disruptions.
Paperwork of upkeep tasks, including solution records and evaluation findings, fosters liability and helps with notified decision-making regarding substitutes and fixings. By focusing on safety nets, companies can guarantee their product packaging makers run at peak efficiency, eventually causing enhanced performance and lowered functional prices.
Conclusion
Finally, the efficient maintenance and fixing of packaging machines are extremely important for maintaining operational efficiency. Normal maintenance minimizes the danger of common concerns, such as irregular sealing and mechanical jams, while systematic troubleshooting strategies help with punctual resolution of malfunctions. In addition, cautious consideration of repair versus substitute choices adds to cost-effective administration of sources. By executing preventive actions, companies can improve equipment long life and ensure uninterrupted efficiency in product packaging operations.
Understanding the intricacies of product packaging machine fixing is vital for keeping ideal efficiency and minimizing disruptions.Regular upkeep of packaging devices is critical for making sure optimal efficiency and durability.Packaging equipments, like any complex equipment, can experience a range of usual issues that might prevent their performance and efficiency. If fixing the machine will certainly create extended hold-ups, spending in a brand-new device that offers enhanced effectiveness and integrity could be much more sensible.In conclusion, the reliable maintenance and repair of packaging devices are paramount for maintaining operational efficiency.